Sprocket Gourmet
by Will Meister
If you're reading this, chances are you're a beginning fixer.
There are several reasons for this. Firstly, sprockets are invisible to the established rider. If you've found your gear and your chainline is set up to your satisfaction, your cog will announce its presence only when it wears out every couple of years. At this point, you will spin off down to the LBS, ask for an exact replacement, and mount up again. Done!
Secondly, most LBSs have a close relationship with one supplier. If they stock fixer kit at all, it will likely be only one brand, and their techs will get used to its foibles. As a result, you will too.
This article attempts to put more choices on the menu. Although it makes no comparisons and only a couple of specific recommendations, it attempts to explain the advantages and disadvantages of different construction methods and designs, and it provides weights and measurements for a shortlist of major suppliers. We aim to maintain and update the list as time goes by.
Cynics please note: 63xc.com has a spinoff mail-order business selling fixed gear components, and we stock several of the brands mentioned here. Caveat emptor.
Daddy's favourite
Sprockets are an old technology, with roots way back in the 19th century. The cog-and-lockring system which you find on most contemporary fixes was established at least 50 years ago, and has remained remarkably consistent. The design is far from perfect, suffering in particular from a tendency of the sprocket to bond to the hub shell under pedalling forces, so that not even a team of mechs using specialist tools can free it. However, even if an alternative technology becomes established in the market, thread-on sprockets are so ubiquitous that, like square-taper BBs and threaded headsets, they will likely be with us for decades to come.
Do fries go with that shake?
The thread-on sprocket predates the ISO era of engineering, and each manufacturer has its own ideas about how to cut a thread. As a result, hub manufacturers often recommend that you use their own brand of sprockets. This is generally an over-reaction: most sprockets will fit on most hubs. But there are certain notoriously bad combinations: Phil Wood hubs really didn't get on with 2000-2003 Surly sprockets, for instance. Before installing a new sprocket, it is therefore wise to take advice from your LBS, mailing list, or hub manufacturer. You might also consider 'opening up' the thread on your new sprocket by oiling it and working it over an old BB cup a few times.
57 varieties
The basic design of the sprocket allows more variation than you might expect. To discuss this, we'd better establish some terminology. The sprocket has a 'shoulder' which carries the thread and to which is attached the plate which has the teeth around its periphery.
Most modern sprockets are made with a single application in mind: a 120mm-spaced track bike with a classic 42mm chainline. They are designed to be installed 'shoulder in, lettering out'. A smart manufacturer will ensure that the 3/32 version of his cog is slightly slimmer than the 1/8 version to allow for the tighter chainline of a 3/32 setup, but that's about as far as the market research goes.
This is dumb. Anyone who has worked on a 130 or 135mm fix will be aware that getting perfect chainline is harder than it ought to be. My own stockpile of vintage components includes cogs from Villiers in the same size but several different configurations, with the plate available at different positions in relation to the shoulder--on the outside, 2mm in, on the centreline... I think that this practice arose when 110mm bikes were still common and the manufacturer had to consider the older spacing as well as the more modern 120mm. It's high time it was revived: it is expensive and timeconsuming to swap out a BB just to finetune a chainline by one or two millimetres.
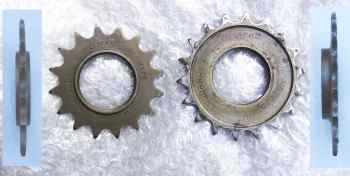
Two Villiers sprockets with end-on views: note the centre-loading of the cog on the left
While I'm at it, I will also mention that 9 and 10spd chains, although nominally 3/32", are actually too narrow to work with many 3/32" sprockets. If you want to try to fix a 9 or 10spd chain, consult the chart to find which the cog with the thinnest teeth, and cross your fingers.
Accept no substitute
There are a number of ways to make a sprocket, but for our purposes we can distinguish two: the right way and the wrong way. The right way is to machine from solid metal, either in one piece (old style) or two (new style). The wrong way is to press-form or lasercut from sheet metal.
Lasercutting was pioneered by a company called Cyclo in the 80s. Although Cyclo had a long and honourable history as a maker of aftermarket components, those sprockets were a bad move. They look the part, but are fatally soft. This means not only rapid wear but also the risk of deformation, and a deformed thread can act on your hub threading like a canopener on a can. One Cyclo user known to me lost his sprocket on a wet day while negotiating a steep downhill at speed in heavy traffic. Think about it.
I've chosen to pillory Cyclo because the company is long-since bankrupt and can't sue me, but similar sprockets are still being sold by a number of retailers who really ought to know better. Although they aren't usually branded, you can spot them pretty easily: the metal looks dull, and the edges of the teeth show a kind of seam. If you are offered one, you are dealing with a shop that doesn't have your best interests at heart. Take your custom elsewhere.
Smooth or crunchy?
Metallurgy is a complex science, and it's probably just as well that most manufacturers don't offer too much information about their manufacturing process--for most people, discussion of RAL numbers and the like will just add to the confusion. But a little bit of extra knowledge goes a long way.
Firstly, consider whether you want steel or alloy.
All manufacturers offer steel sprockets: a few offer aluminium alloys. The alloys don't sell as well, because they are less durable. Although increasingly sophisticated finishing treatments make aluminium more resistant to wear, it remains a relatively soft material and in most commuter/courier applications steel is a better choice. Trackies, for whom longevity isn't such an issue, may prefer to shave an ounce or two.
Secondly, consider carefully the implications of heat treatment.
Materials don't cost much. The steel in your cog was probably cheaper than the packaging in which you bought it. The reason why an ounce or two of metal ended up costing as much as a pair of good jeans was that the manufacturer subjected it to various post-machining treatments to make it wear better.
Durability in a component is a complex phenomenon. Consider a samurai sword.
At its edge, the sword needs to be very hard, to take and hold a keen edge. If the metal at the edge of the sword was soft, the sword would blunt too quickly to be of use.
At its centre, the sword needs to be pliable. This allows it to bend and absorb impact. If the metal in the centre of the sword was hard, the sword would likely shatter against other metal weapons.
The skill of the swordsmith lies in judging hardness and softness and how to combine them.
In just the same way, a sprocket needs hard teeth to withstand wear, but must retain enough pliability to cope with road shocks, sudden changes of speed, and so on.
Case hardening, the deliberate creation of a hard crystalline 'skin' on the outside of a metal component, requires very precise control. Since it isn't economic to process sprockets one by one, they must be batched, and there is then the danger that individual sprockets within a batch may be over- or undercooked. An undertreated sprocket will be too soft and will wear quickly. An overtreated sprocket will be too hard and may shatter in use.
This gives rise to an odd paradox: expensive cogs subjected to serious heat treatment wear better than cheapies, but at an increased risk of sudden failure. Brittle failures are rare, but they do happen, and here is a photo to prove it.
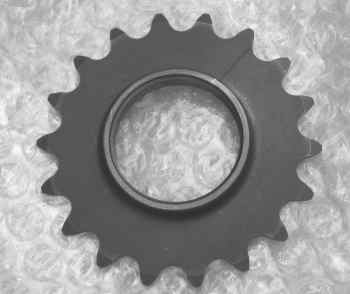
Stress fracture in a cog made brittle by overtreatment. Crack is at 1 o'clock.
On the menu
Here then is our first chart of sprockets. Measurements are firsthand, not supplied by manufacturers. Note that not all of the makes referenced here are available worldwide: some cogs aren't exported. But the chart should provide at least a basic guide to what's on the menu.
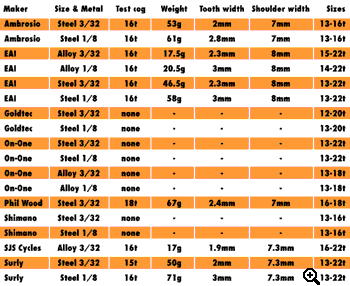
|